Common Auto Welding Mistakes and How to Avoid Them
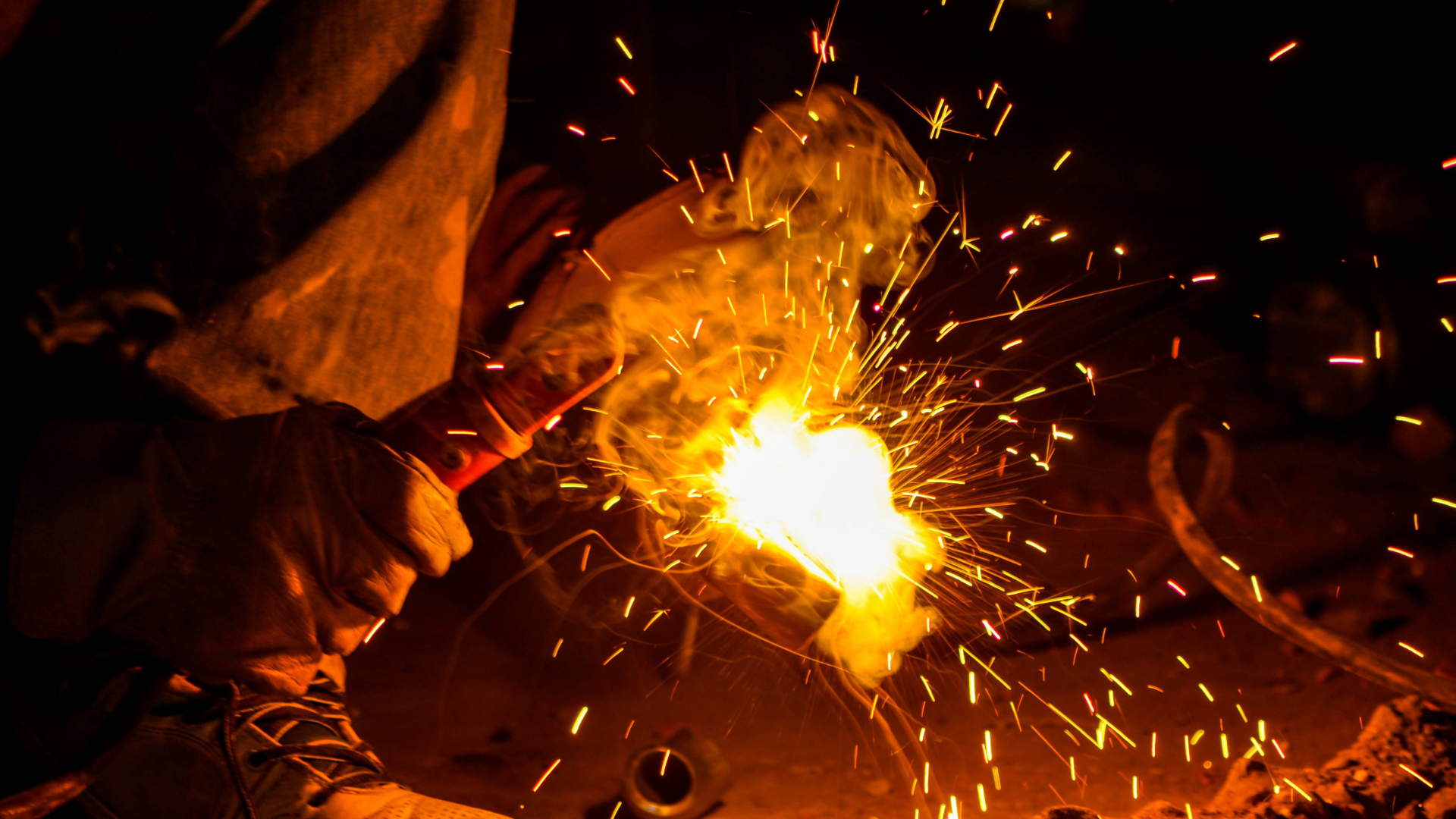
Auto welding can be an incredibly rewarding skill, but it comes with its own set of challenges. Whether you're a novice or have been welding for years, mistakes can happen. The good news is that understanding these common mistakes can help you avoid them in the future. In this blog, we'll take a closer look at some of the most frequent auto welding pitfalls and provide you with tips on how to steer clear of them.
Understanding the Basics of Auto Welding
Before diving into the specifics of avoiding mistakes, it's essential to grasp the basics of auto welding. This includes understanding the types of welding processes typically used, such as MIG and TIG welding, and knowing which one fits your project's needs. MIG welding, for instance, is often favored for its efficiency and ease of use, especially for beginners looking to get their hands dirty with auto restoration projects. However, it is crucial to recognize that each method has its unique advantages and draw backs, which can drastically impact the final quality of the weld. For those eager to deepen their technical knowledge, reading about the most common MIG welding mistakes and ways to rectify them is an excellent starting point.
Understanding the properties of filler metals is another basic yet vital aspect of auto welding. Filler metals are the unsung heroes in many welding scenarios, providing the extra material needed to bind two pieces thoroughly. Nonetheless, not all filler metals are created equal. Depending on the base metals used in your project, the choice of filler metal can significantly influence the strength and longevity of your weld. Investing time to learn about compatible filler materials for the specific metals you are working with can save you from future hassles of weak welds and repairs. Moreover, the role of shielding gases when MIG or TIG welding cannot be overstated. Proper shielding is necessary to protect the weld pool from atmospheric contamination, ensuring a clean and sturdy weld seam.
Using the Wrong Materials
Selecting the incorrect materials for your welding project can lead to weak welds and structural problems. It's not just about the metals you choose for your main structures; every piece of material involved, including the filler wire and the shielding gas, plays a role in the structure's integrity. Using incompatible materials can cause the weld to fail prematurely, potentially leading to costly repairs or worse, safety hazards. A blend of practice and theory is necessary to identify the ideal materials for each job, where services like our Ultimate Guide to Engine Repair provide comprehensive insights into material use and selection processes.
Different projects require different metals depending on their intended applications. Mild steel is often used in everyday car repairs for its vast availability and welding-friendly nature, while stainless steel may be reserved for projects demanding superior anti-corrosive attributes. Likewise, aluminum, which is light and offers excellent thermal conductivity, is often seen in custom car builds but poses challenges due to its low melting point and complicated property changes under heat. Are you intrigued by transforming your ride? You can learn effective techniques and enhance your vehicle's performance by studying our tips and various New Year’s vehicle resolutions.
Neglecting Proper Safety Measures
Safety in welding is paramount. Many welders overlook crucial safety gear and procedures, leading to potential injuries. Unfortunately, neglecting these measures not only threatens the user but also endangers anyone nearby. Protective gear such as welding helmets, gloves, and flame-resistant clothing acts as your first line of defense against burns, sparks, and harmful UV rays. Did you know that exposure to intense ultraviolet and infrared rays without eye protection can lead to "welder's flash" or a painful "arc eye"? Beyond personal protective equipment, the workspace environment also needs special attention, ensuring proper ventilation and removal of flammable materials to prevent accidents.
Poor Preparation of Welding Surfaces
A well-prepared surface is key to a successful weld. Insufficient surface preparation is a frequent oversight that can lead to weak joins or necessitate extensive rewelding. Before striking the arc, spending sufficient time cleaning off rust, oil, paint, and dirt can prevent unwelcome impurities from compromising the weld. Mechanical cleaning methods such as grinding, brushing, and using an abrasive pad can efficiently rid metallic surfaces of blemishes. For an extra layer of cleanliness, consider using a proper degreaser to remove any leftover industrial oils or residues from your pieces.
Moreover, the fitting and alignment of materials should not be underestimated before proceeding with welding. The importance of adequate clamping for holding your work pieces steady during welding should be emphasized to avoid structural misalignment and unwanted movement. Remember, patience and precision during setup can often save hours in corrective post-weld work.
Lack of Experience and Skill
Experience plays a significant role in successful welding. While no one becomes a welding expert overnight, continuous practice, coupled with learning from each missed strike or imperfect bead, is key to honing your welding craft. Participating in a class or workshop targeted toward TIG or MIG welding fundamentals can serve as an excellent foundation for beginners.
Moreover, veterans in the field deal with complex projects but often highlight the enduring value of developing a steady hand and true eye for anticipating weld behaviors under different conditions. Don't shy away from seeking guidance and feedback from seasoned professionals or utilizing resources provided by organizations with tutorials and tips on various welding intricacies.
Ignoring Technical Specifications
Every welding project has its own set of technical specifications that need to be followed closely. Technical readings can sometimes feel monotonous but respecting these blueprints ensures reliability in every joint formed. Overlooking aspects like amperage settings, specific penetration depths, and electrode angles can not only diminish the quality of your results but also lead to repeated failures or adjustments.
Utilizing datasheets can simplify understanding of the technical requirements entailed by your projects. They are invaluable in providing accurate parameters and confirmations to guide your actions. Delve into schematic diagrams paired with relevant standards to align practices with outcomes, all while increasing your proficiency around precise operational procedures.
Master Your Welding Skills
Welding can seem daunting, but avoiding these common mistakes in auto welding will set you up for success. By understanding the process, choosing the right materials, and honing your skills through practice and education, you'll be able to tackle your projects with confidence and precision. For those in need of further assistance or looking to have their vehicles professionally welded, consider visiting us at Auto Express, Sacramento, CA for expert care and service.